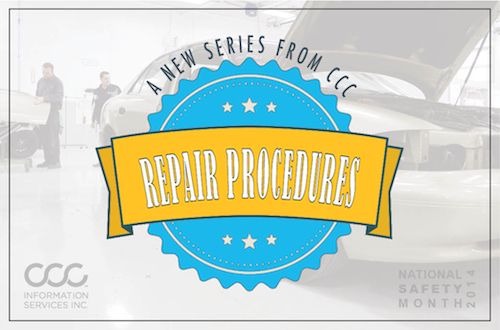
June is National Safety Month, which is the perfect time to talk about the importance of repair procedures! We’ve been on the ground talking to repair shops, insurance companies, and industry experts, and we’re hearing more and more about the importance of using repair procedures—not only to ensure the safety of repairs, but also to improve DRP relationships and profitability for shop owners. That said, there are also challenges that shops face when it comes to incorporating repair procedures into their production process.
We’ve tapped some industry experts to weigh in on this conversation, and the first in this series is Mike Bauer, the founder and Managing Director of thecarpage.com, a resource for automotive industry insight focusing on the changes that technology will have on the automotive industry. Mike brings insights from many years in the technology services industry. Prior to founding the thecarpage.com, Mike led CSC’s global Automotive services team.
What does the future hold for the repair business and will repair procedures keep up?
Vehicles will become increasingly complex and repair procedures will be absolutely critical for success. Changes in electronics, sensor technology, power plants, materials and so forth all spell out a huge change in the repair business. OEM’s will have to work very closely with the repair business and continuously update tools and procedures.
With the changes in materials technology what changes have you noticed?
Right now the repair business is caught between a rock and a hard place. OEM’s legitimately want to certify facilities to benefit their customers. For example with aluminum body panels they often specify one of a kind or proprietary tools. That drives up costs to both consumers and shops. The industry needs to agree on the procedures, tools and techniques amongst themselves, as aluminum and potentially carbon fiber are more mainstream.
Why are repair procedures important? What changes have you seen over the years with adoption?
Collision repair shops are in a tough spot. They’ve got to be able to give an accurate estimate and then to ensure their profitability, they’ve got to be able to meet that estimate. They want to have happy customers, a profitable relationship and also deliver the service that an increasingly demanding consumer population demands.
Repair procedures can help to improve the accuracy of the estimate and the ability to deliver a safe, timely repair. By removing variables in the work they do, repair procedures can also help shops make a reasonable profit on that work.
If you think of the overhead cost of a collision facility, their insurance is very expensive, so the more things they can do and demonstrate to keep their insurance premiums down, the better off they are.
How do repair procedures mitigate risk or improve the safety of collision repairs?
There are several views of safety to consider. Lets start with shop and technician safety. With complex structures, battery packs, etc. following procedures will keep the technicians and the shop safe. Next the safety of the consumer who expects the vehicle will operate as new, with all safety features intact and all systems fully operational. Following procedures is the best way to ensure safety for all. Good procedures should have repair and testing as part of a comprehensive check list. Repair often times it’s the ancillary work that comes about.
Is it common for shops to utilize procedures on every repair?
It’s a mixed bag. Many shops with experienced technicians have adopted their own procedures and they are often viewed as trade secrets. A very experienced technician may not feel they need repair procedures, and an inexperienced technician may not understand their value or be too focused on beating the flat rate. So it can be both inexperience, and too much experience, that lead to the decision to forego procedures.
Do you find that shops are going to multiple sources to access repair procedures?
Yes. Most rely on the assembly diagrams and the workshop manuals from the OEM, but the challenge there is that the OEMs generally focus on design for manufacturing, not for repair. Many also will rely on non-OEM/secondary sources and databases, and it’s not uncommon for them to be toggling to different sources to track down that information. I can see a time when all procedures come with a complete video library.
Is there a perception that repair procedures will negatively impact cycle times if they are used on every repair?
I think that in some cases, there probably is that perception, but I believe that’s an erroneous assumption. The changes in materials and the changes in technology are making repair procedures more and more important.
In the electronics business, entire modules require replacement over repair. Vehicle technology is getting to this point now, where elements have to be replaced completely. It is driving up repair cost and creates complications with disassembly and other aspects of the collision repair.
Do repair procedures help with parts procurement?
Yes. When an estimate is being written, repair procedures give you an indication of which parts are required for the repair—a bill of materials. That is invaluable for ordering parts – it helps you understand which parts you will need before you begin the repair.
Do you have any other perspectives on the collision repair industry and repair procedures?
The biggest challenge in the industry right now, when it comes to repair procedures, has to do with changes in technology–both the material technology and electronic technology. I advise people to use procedures and to leverage procedures in the training of new technicians. When repair procedures don’t work, it’s best to document this and go back to change the procedures.
It’s very important for collision repair shops to go back to the people who write the procedures, the OEM’s, the claims adjusters, etc., and communicate their experiences with procedures. That collaborative nature of modern business that has to go all the way down to the smallest repair shop. In the end, what that’s going to do is improve the customer satisfaction and the profitability.
It’s a delicate balancing act. I think the collaborative nature, especially with the electronic tools we have, the collaborative nature of business today has to be fully embraced by the repair shops. It’s for the safety of their employees and the safety of the consumers.